The maintenance procedures required for each
injection molding location depend on different mold cycles. Below are some general principles that every mold user can use to ensure the efficient operation of mold components such as hot runners, heaters, guide posts, and ejector pins, in case the unexpected arises.
1. Look for early warning rust or dampness at the vents – if you find rust or dampness near the hot runner vents, it means there is condensation inside or maybe the water pipe is broken. Moisture can cause a fatal short circuit to the heater. If the machine is not running all year round but is shut down at night or on weekends, the chance of this condensation will increase.
2. Remember to remind the operator not to "clean" the hot nozzle at the gate - if the operator happens to see a small piece of stainless steel at the mold nozzle, it may actually be a nozzle component. "Cleaning" out what appears to be a hindrance often destroys the hot tip. In order not to destroy the hot nozzle, please confirm the nozzle type of the lower hot runner system before taking action, make sure that all operators are well trained and can identify all the different nozzle types they come into contact with.
3. Skid stop – This should be done weekly for machines that run year-round.
4. Cross-check heater resistance – You should have measured the resistance of the heater when you first started using it, now it’s time to measure again and compare. If the resistance value fluctuates by 10%, it is time to consider replacing the heater to ensure that it does not fail at a critical point in the production process. If the initial resistance value has never been measured, measure it now and use the resulting value as a reference for future inspections of the heater.
5. Look for signs of wear between the guide post and guide bush - look for signs of scratches or scuffs, which are due to lack of lubrication. If the marks are just emerging, you can also extend the life of the guide posts and guide bushes by lubricating them more. If the wear is severe, it is time to replace the parts with new ones. Otherwise, the cavity and core parts may not fit well, resulting in different thicknesses of the part cavity walls.
6. Check the water flow – connect a hose to the outlet of the waterway and let the water pass through the hose to the bucket. If the water flowing out is not clear or colored, rust may occur, and if the water is not flowing smoothly, it means that there is a blockage somewhere. If these problems are found, re-drill all the pipes to make sure they are clear (or clean them by whatever method you use most often). Improving the plant's water treatment system can prevent future problems caused by rust and blockages.
7. Clean the thimble – Over the course of a year, the thimble can get dirty due to gas build-up and membranous impurities. A good cleaning with mold cleaner every six to twelve months is recommended. After cleaning, apply a layer of lubricant to the thimble to prevent chafing or breaking.
8. Check the radius area of the nozzle for cracks - the cracks are caused by the clamping force from the barrel assembly of loose, hardened plastic debris left in the machine nozzle during forwarding injection. It is also possible that the problem is caused by the misalignment of the centerlines. Both possibilities are to be considered when finding fractures. The sprue bush should be replaced if the damage has been severe enough to prevent petal leaks (a term formerly used by mold users: plastic leaks between the guide bush and the hot tip of the machine).
1210 PALLET MOULD GRID DOUBLE-DECK WELDING TYPE PALLET
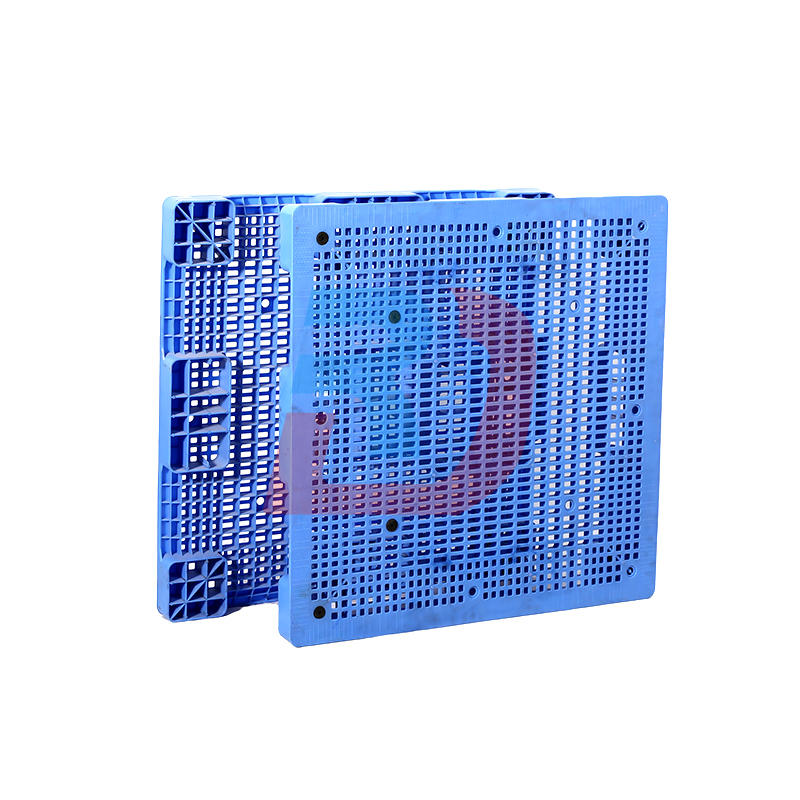
Mould Name 1210 Pallet Mould
Product Size 1200*1000*150/160mm
Product Description Grid Double-deck Welding type Pallet
Mould Size 1580*1750*850/880mm
Mould Cavity 1 cavity
Product Material HDPE
Product Weight 11.5kg
Mould Injection System 20 tips China Brand Hot Runner
Mould Ejetion System Ejector Pin & Ejector Plate
Mould Cycle Time 75s
Cor/Cav Mould Steel Pre-hardened P20 with forging technology & HRC38-45°
Interchangeable Block & Slider Steel Pre-hardened 718H with HRC36-40°
Mould Components DME/HASCO standard parts.
Mould Life Guarantee 1 Million Shots
Hydraulic Cylinder Made in Taiwan
Surface Treatment Polishing/Texture
Delivery Time 70 Working Days