Designing nine foot pallet moulds with durability in mind is essential to ensure their long-term performance and reliable production of sturdy pallets. Here are some key factors to consider when designing for durability in nine foot pallet moulds:
Material selection: Choose high-quality materials that can withstand the demanding conditions of pallet production. Opt for durable and corrosion-resistant materials such as hardened steel or other suitable alloys. The selected materials should have excellent strength, wear resistance, and dimensional stability to withstand the pressures and forces exerted during the moulding process.
Robust construction: Ensure that the mould's construction is robust and capable of withstanding repeated use and heavy loads. Reinforce critical areas prone to stress, such as the corner joints, supports, and ribs. Incorporate adequate reinforcement and bracing to prevent deformation, warping, or failure under load. A well-constructed mould will maintain its integrity and shape over time.
Proper wall thickness: Determine the appropriate wall thickness for the mould components, considering factors such as material properties, mould size, and intended load capacity. A sufficient wall thickness is crucial for structural integrity and resistance against deformation or breakage during the moulding process. Balancing the thickness will ensure durability without unnecessary bulk or weight.
Reinforcement features: Incorporate reinforcement features into the mould design to enhance durability. These can include ribbing, gussets, or support structures strategically placed to strengthen areas prone to stress or wear. Reinforcements distribute forces evenly and help prevent stress concentration, extending the mould's lifespan.
Smooth and durable surfaces: Ensure that the surfaces of the mould components are smooth, resistant to wear, and easily cleanable. Smooth surfaces reduce friction during the pallet moulding process and minimize the risk of pallet imperfections. Consider surface treatments or coatings that enhance durability and prevent damage from friction, abrasion, or chemical exposure.
Heat and cooling management: Efficient heat and cooling management is crucial for durability in pallet moulds. Incorporate proper cooling channels or systems to ensure consistent and controlled cooling of the mould during the moulding process. This helps prevent overheating, warping, or degradation of the mould over time. Effective heat management ensures reliable and consistent pallet production.
Alignment and precision: Precise alignment of mould components is essential for durability. Accurate machining and assembly techniques are necessary to ensure proper fit and alignment. Misalignment can lead to premature wear, excessive stress, or inconsistent pallet quality. Use advanced manufacturing processes and quality control measures to achieve precise alignment and maintain the longevity of the mould.
Regular maintenance and cleaning: Establish a routine maintenance and cleaning schedule to keep the nine foot pallet mould in optimal condition. Regular inspection, cleaning, and lubrication help prevent build-up, corrosion, or damage that can compromise the mould's durability and performance. Follow manufacturer recommendations for maintenance practices to ensure longevity.
Testing and optimization: Perform thorough testing and optimization during the design and prototyping phases. Test the mould design under realistic operating conditions, considering factors such as load capacity, stress distribution, and material flow. Analyze the results and make necessary adjustments to optimize the design for durability and performance.
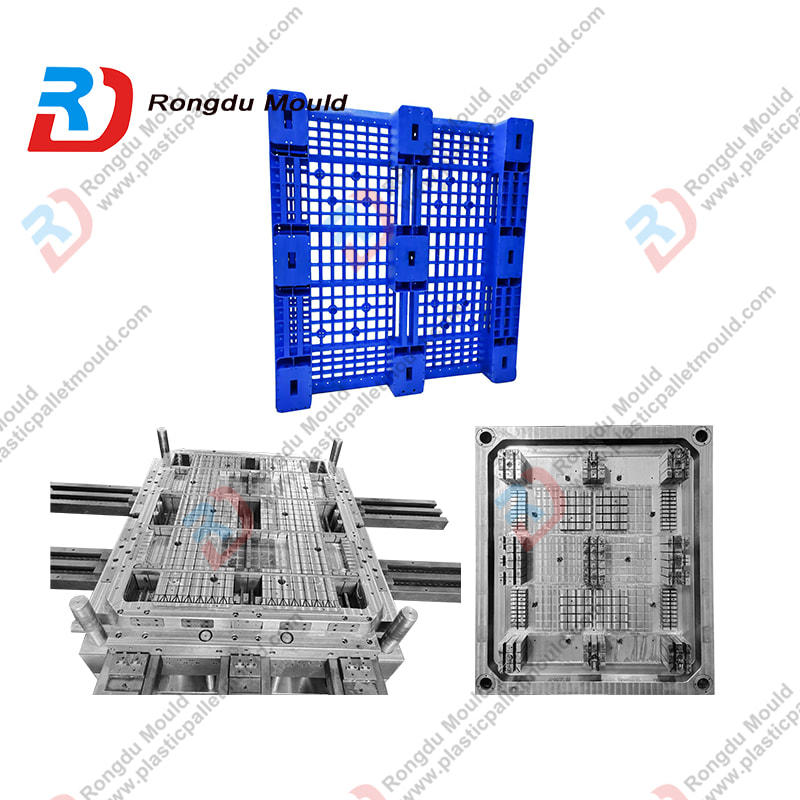
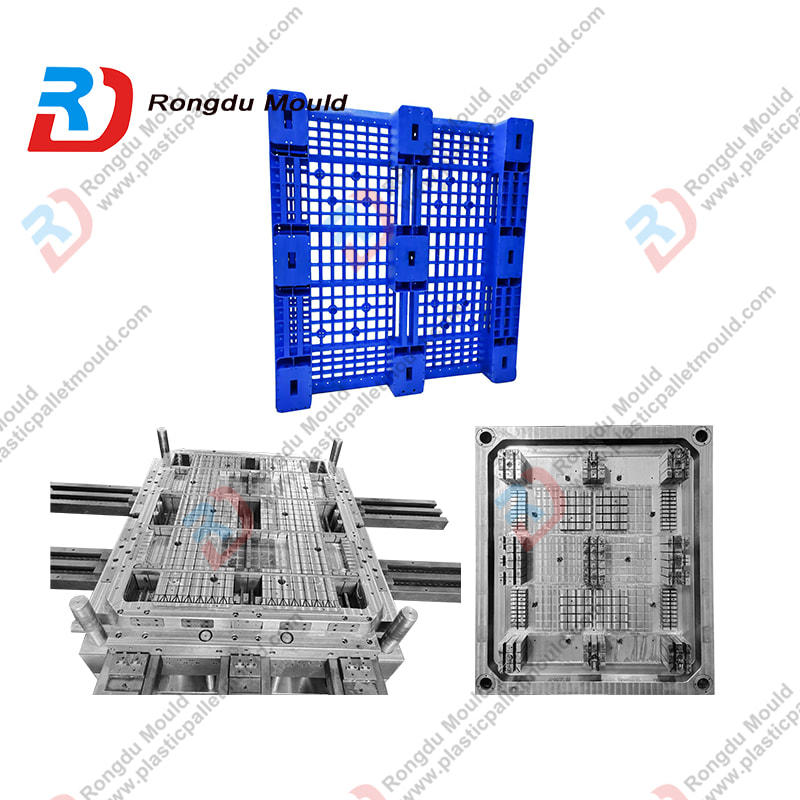
By considering these factors during the design process, you can ensure the sturdy construction of nine foot pallet moulds. Durability in these moulds is essential to withstand the demanding conditions of pallet production, provide reliable performance, and contribute to the production of high-quality and long-lasting pallets.